APQP(Advanced Product Quality Planning) 是在汽车和制造行业中确保产品在开发和生产过程中质量和可靠性的方法和框架。本文将深入探讨APQP的历史、全球标准以及它的五个关键阶段。
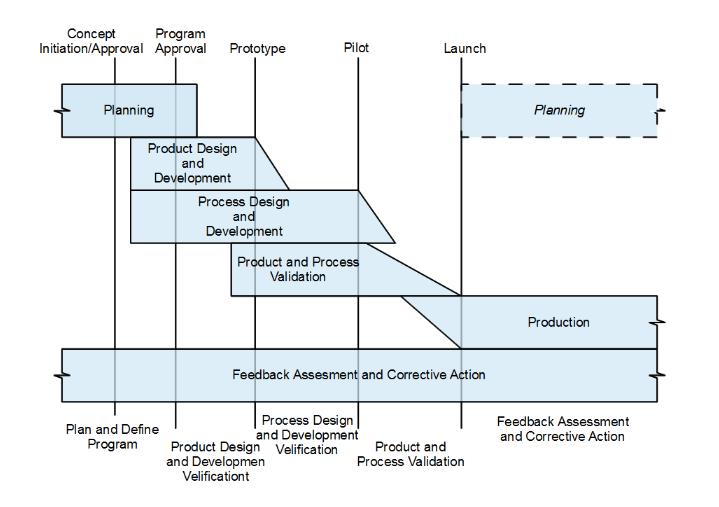
了解APQP
APQP的核心在于理解和满足客户期望,这是任何业务成功的关键要素。通过将质量纳入设计过程并在零部件到位之前减轻生产过程中的风险,APQP能够实现更可预测的商业成功,提高客户满意度,改善客户忠诚度并提高业务竞争力。
APQP的历史
起初在80年代晚期引入,APQP计划最初由汽车行业的主要原始设备制造商(OEMs)采用,包括通用汽车、福特和克莱斯勒。它们认识到为供应商制定一套共同的产品质量规划原则的重要性,尤其是在汽车制造中的供应链中。随后,在90年代初,建立了标准指南以增强对APQP协议的遵守,自此以后,APQP过程逐渐在全球范围内流行开来。
APQP的全球标准
多个组织在全球范围内制定了与APQP相关的标准,其中最广泛采用的包括:
- 美国 - 汽车工业行动小组(AIAG)
- 德国 - 德国汽车工业协会(VDA)
- 日本 - 日本汽车制造商协会(JAMA)
制造商何时启动APQP过程?
在启动APQP之前,制造商应进行可行性评估,确保未来能够确保客户成功。这需要考虑技术能力、生产能力、供应链、质量能力、财务稳定性、时间和交货周期、客户关系以及风险水平等因素。只有在可行性被证实的情况下,他们才应该进一步进行。
APQP的五个阶段:综合概览
阶段1:规划和程序定义
在引入新产品或对现有产品进行全面翻新之前,必须进行初步规划。这一阶段的关键任务包括了解产品的客户需求和期望,以及为制造指定产品而定义产品设计、可靠性目标、质量目标等的数据收集。
阶段2:产品设计和开发
这一阶段侧重于完成产品设计,适用于公司负责产品设计的情况。关键输出包括设计失效模式效应分析(DFMEA)、设计用于制造和装配、设计审查和验证等。
阶段3:过程设计和开发
该阶段集中于规划生产新产品或改进产品所需的制造过程。关键交付包括包装标准/规范、完全定义的流程流程图、生产楼层平面布局、特征矩阵、过程失效模式效应分析等。
阶段4:产品和过程验证
在这一阶段,进行产品和制造过程的验证,确保它们符合规范、质量标准和成本效益。关键交付包括测量系统分析计划、初步过程能力研究等。
阶段5:生产启动、评估和持续改进
生产启动后,进行评估并持续改进。这一阶段确保产品在实际生产环境中仍然符合质量和可靠性要求。
结论
APQP是确保产品质量的关键方法,通过其五个阶段的结构性过程,帮助企业最大化客户满意度、提高竞争力并降低成本。这是一种在不断创新和增强产品压力下的行业中,尤其有益的方法。